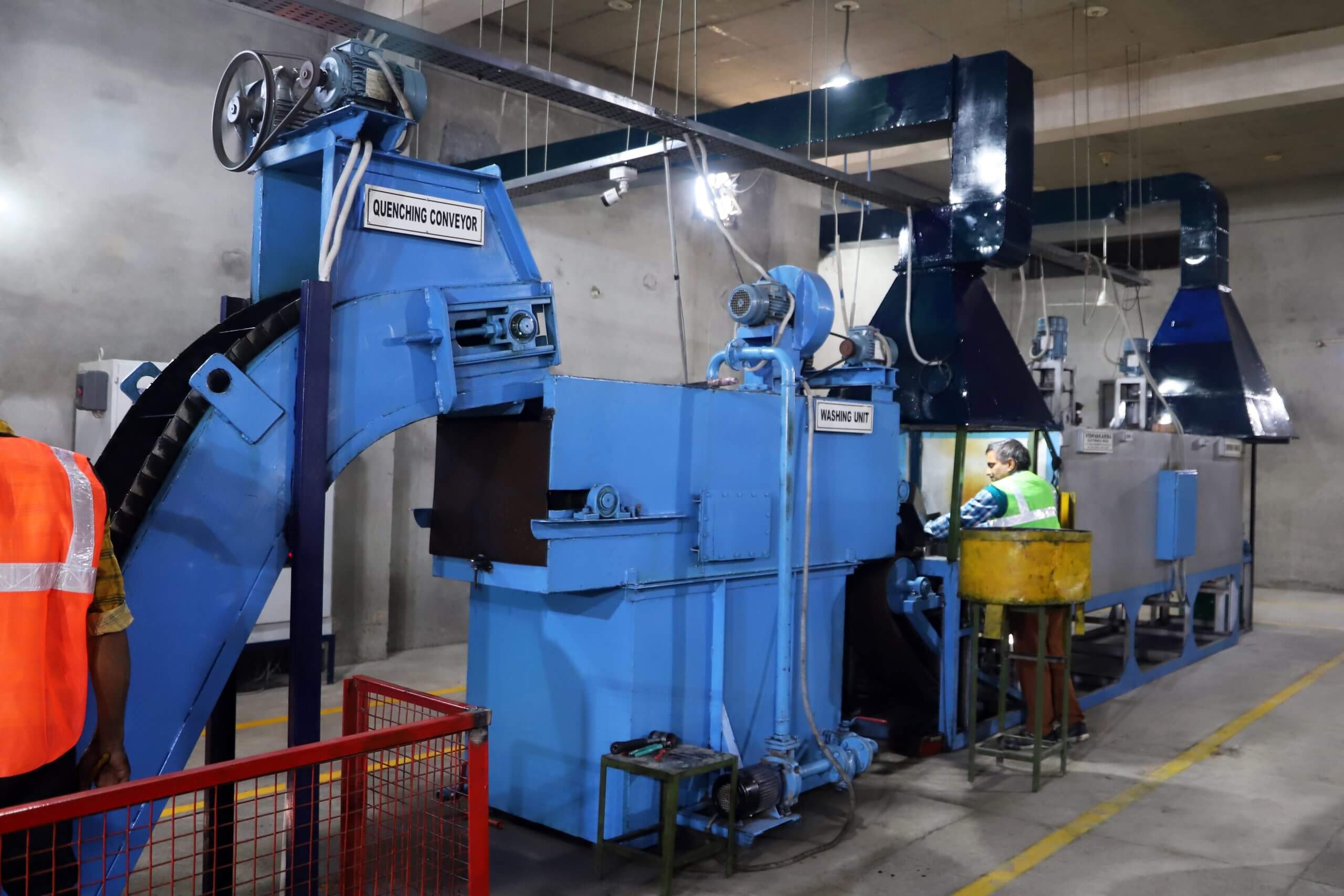
QUALITY YOU CAN RELY ON
Every circlip we produce reflects our dedication to precision engineering and rigorous quality control.
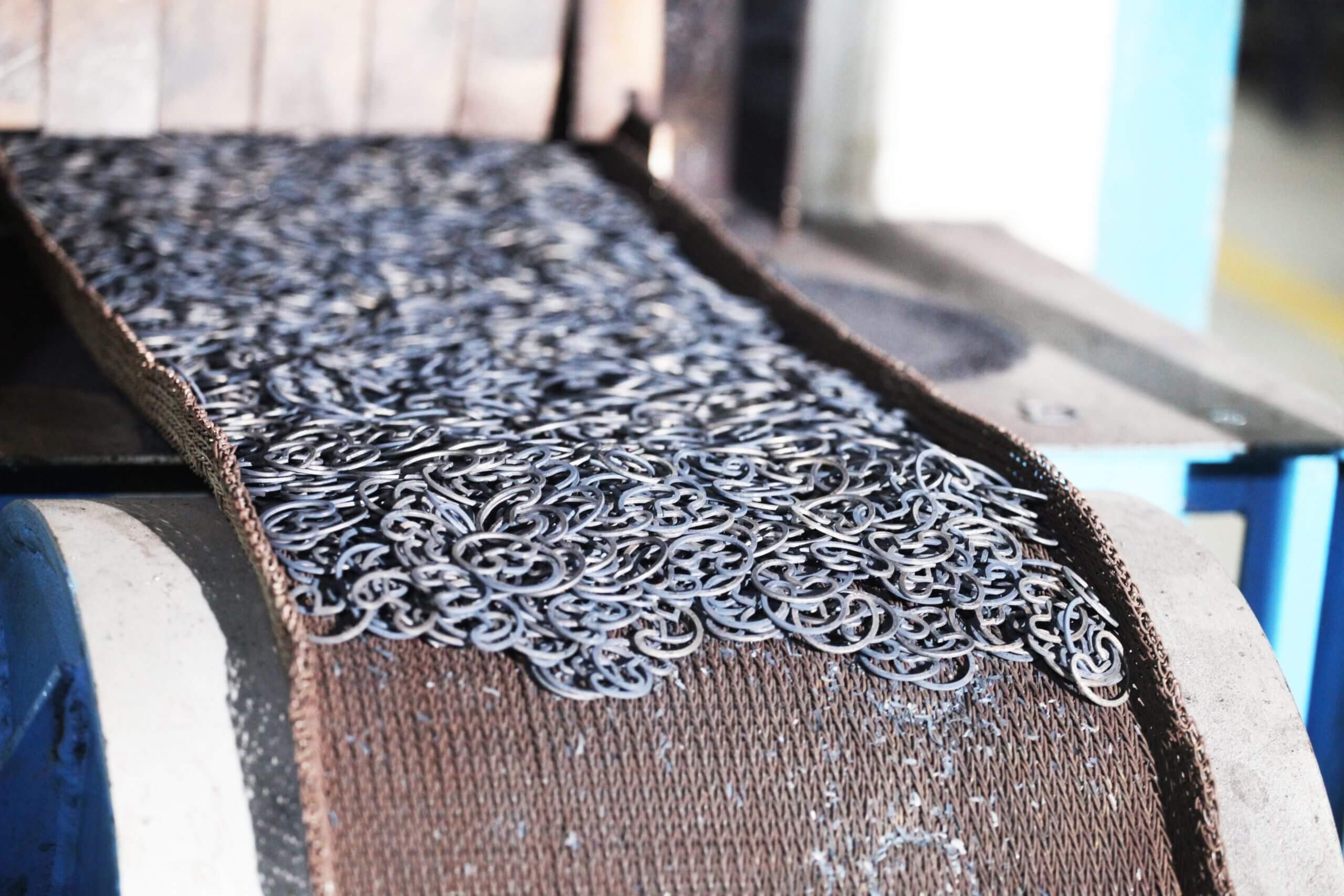
Commitment to Quality
Delivering precision, reliability, and excellence in every component we manufacture.
Quality Excellence
Customer satisfaction is our highest priority, achieved through the continual improvement of our processes, products and skill matrix. We actively engage our entire workforce with the aim of delivering maximum value to our customers.
We adhere to strict quality control standards at every stage of production. Our commitment to precision ensures every part meets the highest industry benchmarks.
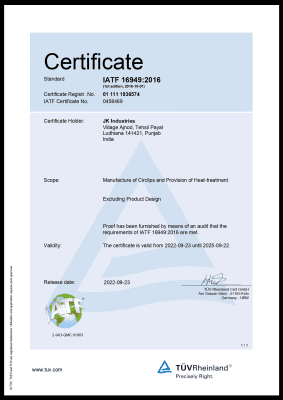
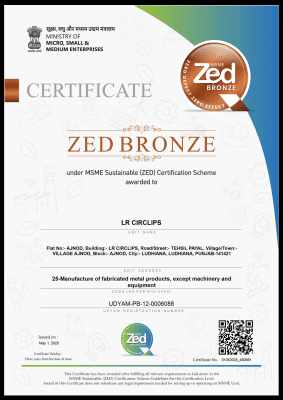